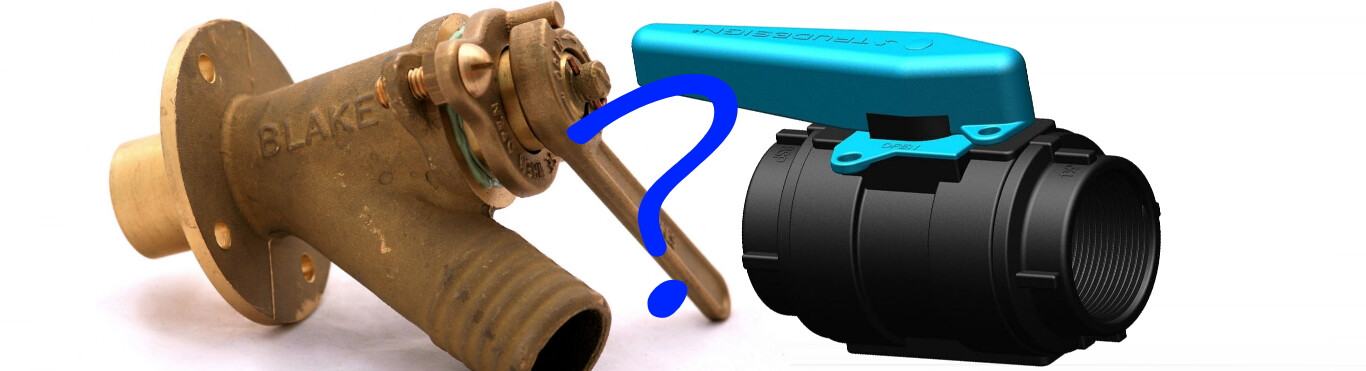
Should we upgrade to composite skin fittings?
Maintenance can sometimes seem pretty endless when it comes to owning a boat, and our time is precious. We want to maximise our time afloat while minimising our winter maintenance. So should we be looking at upgrading our skin fittings? It’s a job that could take a few days to complete, but could save your boat (and possibly crew) so we thought we’d look at why you might want to do it and what the possible advantages are…
The Through Hull Fitting Explained
Through Hull fittings normally consist of 3 items, the skin fitting itself, the ball valve (that can seal off the skin fitting) and a hose tail that then attaches to a hose and runs off to whatever appliance it is connected to.
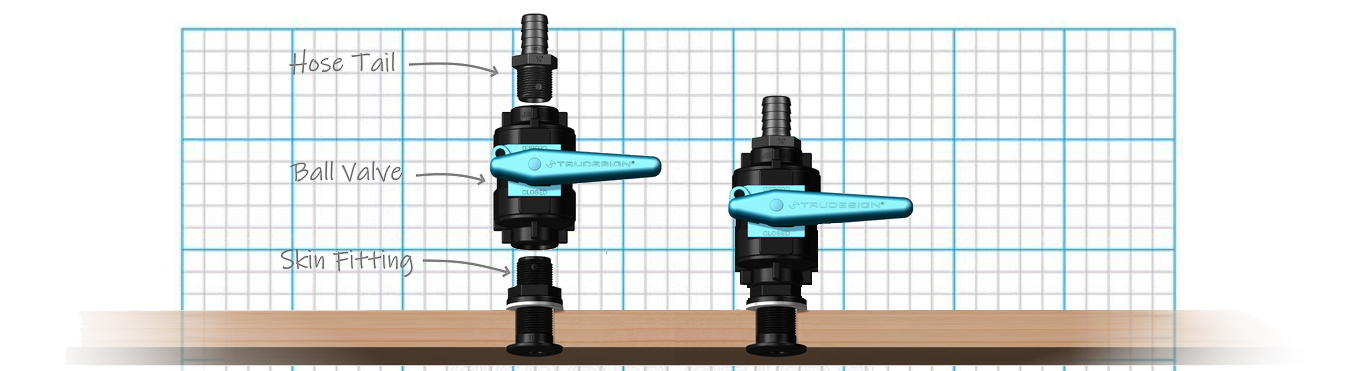
Your existing Through Hull Fittings
Most people have no idea what skin fittings they have installed on their boats, but there are certain things we can assume and other things we can deduce by looking at both our boat and the skin fittings to see whether it’s worth replacing them. What we do know is that a catastrophic failure of either a skin fitting or seacock can cause the boat to sink, so a bit of investigation is a good place to start and can pay dividends.
The first thing to check is what material they are made of. Skin fittings often have marks moulded into them that tell us what material they are made of, they may not seem obvious at first, but if you find any markings, and a manufacturer's name, the internet can often reveal what they are made of. What we are trying to ascertain is what type of metal they are made of. If it’s a basic brass, then these can essentially corrode from the inside out, the damage being almost invisible until it’s too late. We recommend changing these almost regardless of age. Brass skin fittings & seacocks were commonly used on many production boats built from around the turn of the century onward (before the major dangers of this type of material were fully realised), so the age of your boat can be an indicator, although it is by no means decisive. If in doubt, assume brass unless you can prove otherwise. DZR (or de-zincified brass) is another material that your seacocks and skin fittings could be made from. DZR is superior to brass, but we still recommend precautionary replacement at around 10 years old, so again, if you’re not sure, replace. If you are lucky enough to have bronze skin fittings, these can be relied on to a much greater extent, but ball valves are rarely made entirely from this material, and often have chromed ‘balls’ and teflon inserts, so with these we would be more tempted to go off the condition than the age. Do they turn easily? Are the handles in good condition, or looking a little worse for wear? With all seacocks, regardless of age, and at the very least, a gentle but firm tap with a mallet can certainly reveal if the fitting is on the edge of a catastrophic failure...
Composite or metal?
When looking to replace, you have 3 main choices; DZR, Bronze or Composite. Here at Force 4 we sell all varieties, but our recommendation is moving firmly in the direction of composite fittings. If you do decide to replace with DZR, bear in mind that the lifespan of this material is around 5 years. Bronze, being superior, is also naturally more expensive, and if you do go down this route ensure you keep receipts in your vessels paperwork file to prove the provenance of the fittings to any future owner. Composite fittings are essentially made from a similar material to the boat itself, so strength really isn’t an issue, and are described by the manufacturer as ‘fit for the life of the vessel’. The main issue with all metal fittings, corrosion, suddenly goes out of the window, and composite fittings are easily identifiable by the obvious differences in their appearance. Our best selling composite skin fittings, Tru Design, are approved by many organisations such as ISO, Bureau Veritas, CE, and ABYC to name but a few. Composite fittings are flame retardant, so can be used in engine rooms and machinery spaces, and are also incredibly UV stable, not that this is an issue in most installation environments.
The Installation Process
Installing new seacocks is reasonably easy, removing the old ones is often the hard part! One saviour during this process is that we aren’t trying to save the old fittings, so in the worst case an angle grinder may need to be employed. In the main though these fittings will unscrew with the use of a reasonable amount of force and patience. The main thing when removing old skin fittings is to make sure that you avoid damage to the surrounding hull. Do not use heat as you would when trying to loosen other threaded metal fittings (you can cool however), and take your time - this is not a process to rush.
Installing new composite fittings is easy, threads and hole diameters should be the same as with your old metal fittings, so the new fitting should fit the existing holes. Ensure that the hull is clear of antifoul, primer and other dirt on both the inside and outside of the hull. Plan the installation by dry fitting everything (including the ball valve) to check clearances and that the handle turns freely and is not obstructed. The skin fitting can be cut to length with a hacksaw if required. When you are satisfied that all is well, apply a health bead of some underwater bedding compound such as Sika 291i or 3M 3200 sealant to the mating surface of the fitting. Put it in place and apply another bead of sealant to the inside of the hull. Install the fitting, add the washer to the inside and hand tighten the backing nut. Remove any excess sealant now before it dries and becomes very difficult to remove. Allow the sealant to dry before coming back and fully tightening the backing nut - sealant doesn’t work when it’s all squeezed out during the tightening process, then move to the next part of the system and install the ball valve and hose tail.
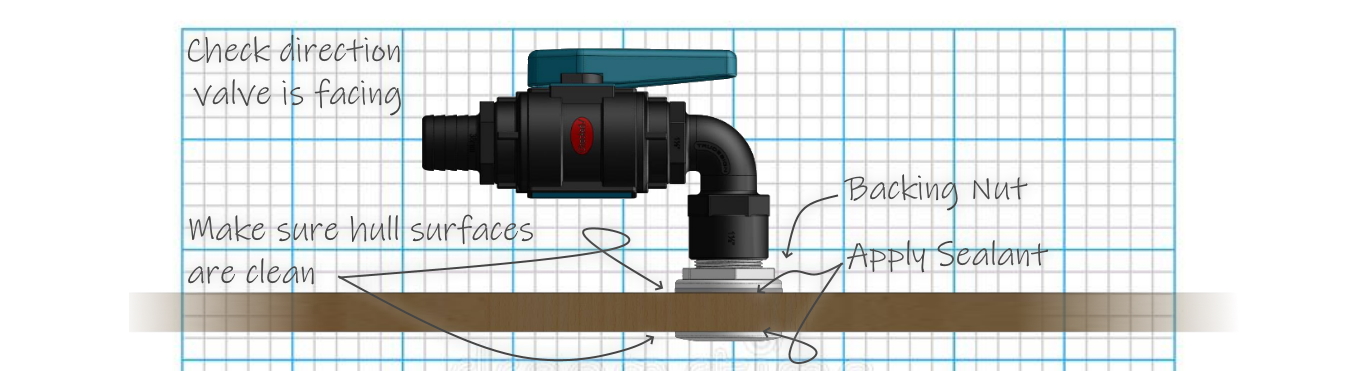
Tru Design Skin Fitting Components
BALL VALVES (SEACOCKS)
The key product in their range, the ball valve controls thru-hull inlet and outlet requirements. The ball and seal ring are moulded in a PTFE filled polymer for lubricated, smooth continuous ease of operation. This material resists marine growth, such as barnacles, from seizing up the valve. Plus, they’re frost-friendly so won’t split like metallic ball valves when frozen.
- Individually leak & pressure tested during manufacture
- OPEN/CLOSED positions marked for easy identification
- Certified to ISO 9093-2 by Bureau Veritas & IMCI
SKIN FITTINGS
Compatible with all hull types (wood, steel, composite, GRP, aluminium), they are available with a traditional dome shaped head or a countersunk head for a streamlined finish, thus reducing drag and the possibility of snagging.
- Chemical resistant – unaffected by antifouling, diesel, petrol
- UV resistant
- Suitable from -40°C to +110°C
HOSE CONNECTORS
A range of straight, 90° and 120° connectors giving a strong, secure connection with reliable waterproof sealing in any situation.
- Chemical resistant
- Designed for twin hose clips & will not crush